Are your bolting methods safe?
Industrial bolting can become a safety issue with costly consequences when dealing with large, bulky products requiring heavy equipment. HYTORC eliminates the pinch points that cause common hand and finger injuries. Hand safety is paramount in industrial bolting.
Read this article to avoid costly mistakes for your company.
WHAT’S AT STAKE?
While 27% of all occupational injuries are related to hands and fingers in the regular workplace, the numbers are increasing in heavy industry. For example, the International Association of Drilling Contractors reported that 43% of all injuries in the oil and gas industry are caused to workers’ hands and fingers.
From broken bones to mutilating, crushing and debilitating injuries, the ensuing investigations can cause a plant or refinery to shut down production for an entire year.
DOWNLOAD your Hand Safety White Paper
SAFETY PROBLEMS IN THE WORKPLACE: What’s the cost?
A hand injury can cost between $50,000 and $250,000 in losses, not including the resulting lawsuit. The U.S. Bureau of Labor Statistics reports that the average number of hand injury claims now exceeds $6,000, with each claim resulting in nearly $7,500 in lost time. Hand injury investigations can shut down a plant or refinery for an entire year, easily resulting in millions of dollars in lost revenue.
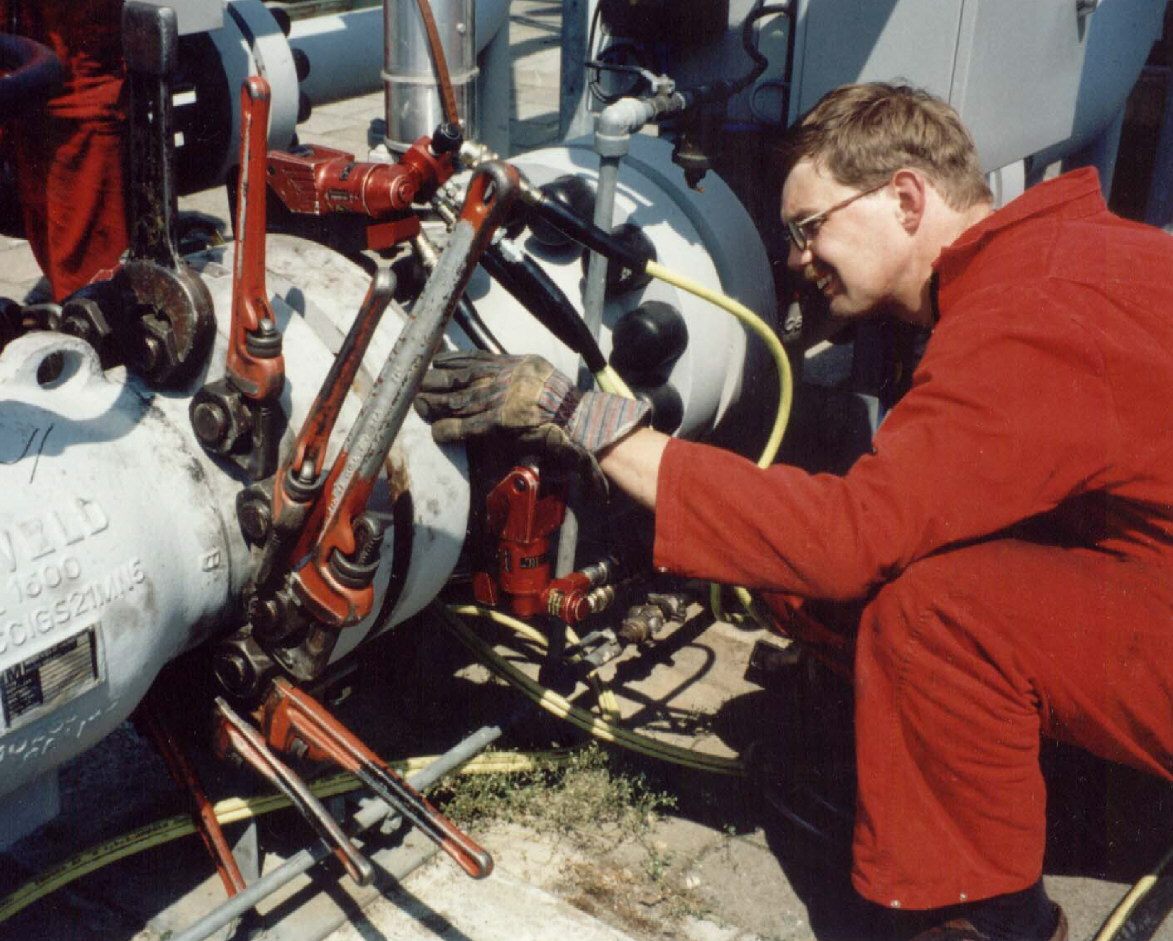
SAFETY IN THE WORKPLACE: What’s the solution?
Eliminate pinch points with the unique REACTION FREE ARM and BACKUP WRENCH bolting solution.
The HYTORC “washer” also eliminates the complex set-up usually associated with other bolting systems, and makes the bolting process more intuitive to improve working times.